Carol Johnson, Southern Indiana Business Report
MITCHELL – A new plant with a new name is charting a new future for a leader in cement production in Mitchell.
Heidelberg Materials invested more than $600 million to build a new plant at the former Lehigh site that significantly reduced its carbon dioxide emissions and energy consumption while also increasing production levels.
On Tuesday, Heidelberg Materials celebrated the opening with a ribbon cutting at the Mitchell plant. The large gathering of guests included federal, state and local leaders.

“Our Mitchell project instills pride in our rich history and provides an exciting look into the future of cement production at the same time,” said Heidelberg Materials CEO Dominik von Achten. “The plant will substantially contribute to Heidelberg Materials’ offering of low-carbon cement and concrete – it is the springboard to becoming the first fully decarbonized cement plant in the U.S. It represents our commitment to further strengthening our North American footprint and increasing the sustainability of our products.”
Construction took place over 2.5 years and included a new kiln and storage dome. About 1,000 construction workers were employed during the project.
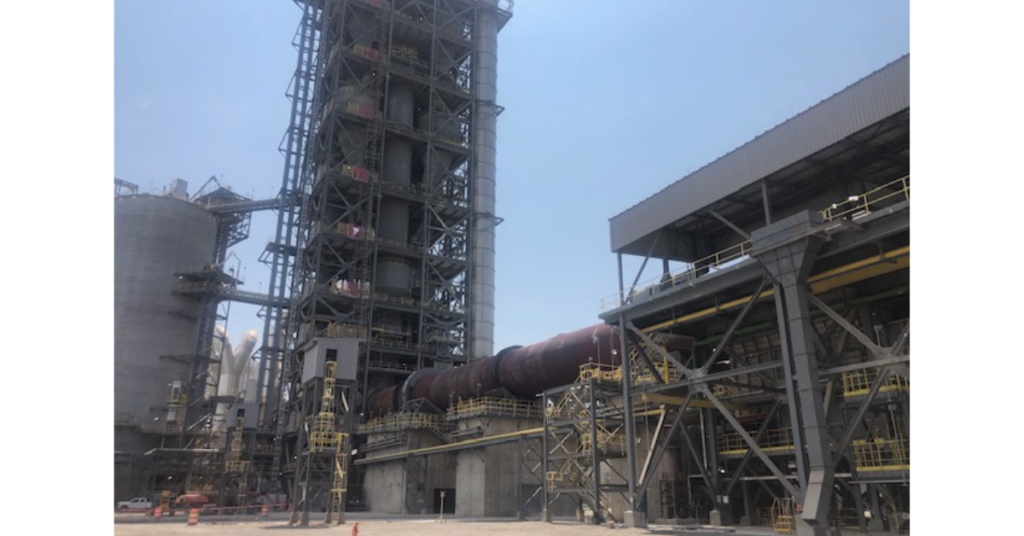
The new Mitchell plant has advanced technology and design features to meet ambitious production and capacity goals. A new automated lab, a smart motor control center to collect and communicate data, and a high-speed automated rotary-type packing machine capable of filling 3,600 full-sized (94-pound) bags per hour will dramatically increase efficiency.
The Mitchell plant will be capable of producing more than 2.4 million tons of cement a year and is expected to help address U.S. cement supply chain constraints. It opens on the heels of the 2021 passage of the Infrastructure Investment and Jobs Act. This federal legislation, among other things, provides funding for surface transportation needs, including $110 billion to repair roads, bridges and support major infrastructure projects.

During construction, it became apparent the new plant was vastly different when the immense dome emerged on the horizon. The dome is a 219-foot-wide, 164-foot-high storage dome, which can hold 154,000 tons of clinker, the intermediate material produced in the manufacture of Portland cement. The structure was built with Heidelberg Materials’ EcoCem PLC TM the company’s lower-carbon Portland Limestone Cement, and is the largest dome constructed of this product in North America.
Innovators for more than 100 years
The Mitchell plant has been in operation since 1902. Plant manager Tracy Crowther said generations of Mitchell area residents have worked at the plant to provide construction materials to southern Indiana.
David Rosenberg, COO of the Indiana Economic Development Corp., said Heidelberg’s investment is an example of the innovation that is helping create the economy of the future in Indiana.
“I jumped at the chance to be here today because our partnership with future-focused businesses like Heidelberg are exactly how we’re going to build that economy of the future,” Rosenberg said. “Global industry leaders like Heidelberg are leading the way, advancing our high tech opportunities creating innovative solutions to tackle the global energy transition.”
Among the many improvements to production volume and efficiencies, the Heidelberg management team touted the plant’s reduced emissions as a tremendous step forward.
“The plant will reduce clinker production carbon dioxide emissions per ton of product by almost 30% mainly through operating on natural gas,” said Chris Ward, president and CEO of Heidelberg Materials North America.
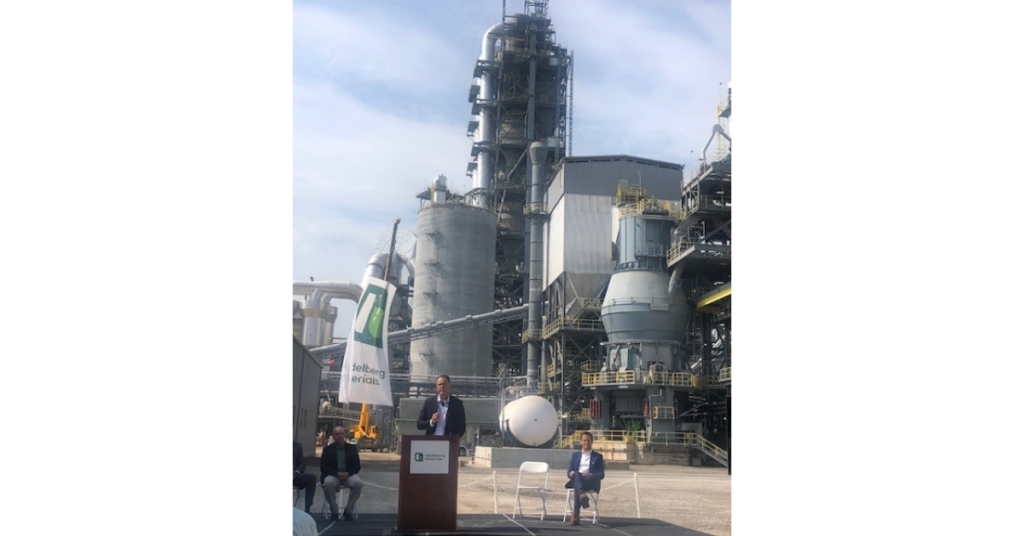
The new facility will primarily produce EcoCemTM PLC, the company’s durable cement produced with a significantly smaller carbon footprint. Additionally, Heidelberg Materials is leveraging funding from the U.S. Department of Energy at the site to study the feasibility of carbon capture, utilization and storage (CCUS) at the site.
Heidelberg has set a goal of fully de-carbonizing the plant by 2030.
“We strongly believe in the local team here in Lawrence County and we want this to be the most sustainable plant,” said von Achten.
Product distribution was also improved. With the increased capacity, the plant will bring on an additional 1,000 rail cars to serve the newly renovated rail yard near the site. The new distribution terminal accommodates 32,000 tons of additional cement storage.
Plant tours
Following the remarks, which also included recorded messages from Gov. Eric Holcomb, Sen. Todd Young, Sen. Mike Braun and State Rep. Erin Houchin, guests were given plant tours.
Many people confuse cement with concrete and mistakenly think they are one and the same.
Mitchell Cement Plant project engineer Ian Nelson explained that cement is a powder that is mixed with aggregates to make concrete.
“Think of it as the flour of a cake,” Nelson said.
The process of making cement starts with limestone quarried that is crushed and then run through a kiln to produce clinker. The plant makes different types of cement to match customer specifications. Nelson said quality is monitored regularly by automated samplers.
Non-potable water used in the process comes from an old quarry on the site as well as a cave source in Spring Mill State Park.
A new kiln that runs 24/7 and reaches an internal temperature of 2,000 degrees has an increased capacity that will replace seven Heidelberg kilns in Indiana that aren’t as efficient.
Fifty new full-time jobs will be added to the plant, which employed 120. The plant employs a wide range of skills including yard laborers, electricians, millwrights, engineers and chemists.