VUJC one of eight sites in state offering paid skills program
Carol Johnson, Southern Indiana Business Report
JASPER – Indiana is second in the nation in overall automotive production, producing 1.3 million cars and trucks a year. One in five Hoosiers works in advanced manufacturing and 25% of the state’s economic output comes from manufacturing.
Even as technology and automation alter the manufacturing landscape, skilled workers remain essential — and in short supply.
The state is taking steps to make sure the workforce has the necessary skills for today’s advanced manufacturing.
Catapult Indiana is preparing unemployed and underemployed adults as well as high school students for new careers through classroom and hands-on simulations.
Catapult was launched statewide in 2019 by Conexus Indiana, a nonprofit that works to improve the state’s advanced manufacturing workforce. Catapult has eight programs around the state and two more are in the works.
To date, the program has a 70% graduation rate and 90% job placement for graduates. On average, they earn $18/hour average for full-time employment.
Five students from Daviess and Martin counties recently completed Catapult at the Vincennes University Jasper Campus.
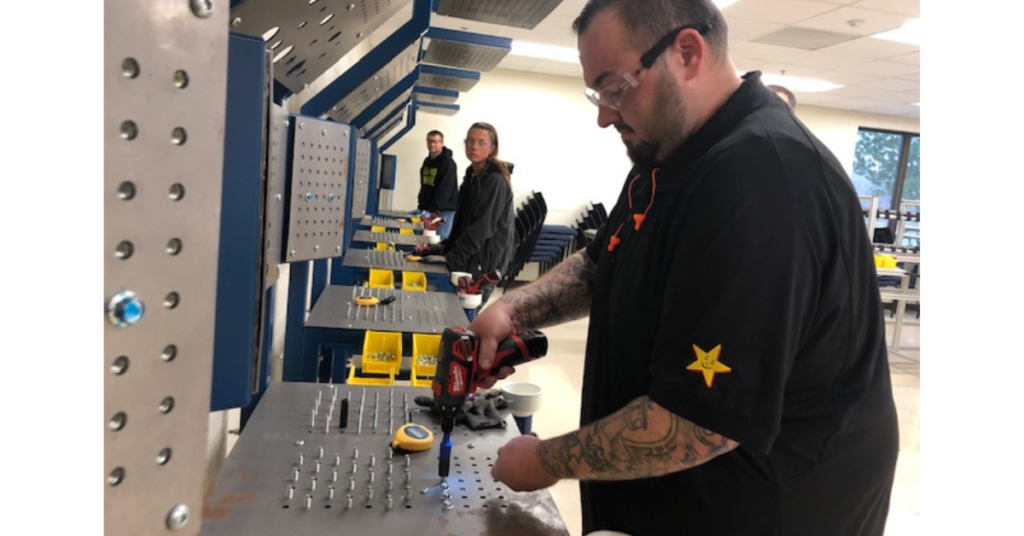
Over four weeks, the students received 160 hours of instruction in advanced manufacturing. Catapult instructor Paul Mullis, who also teaches the program at Branchville Correctional Facility, provided oversight.
In this class, all the students were justice-involved and referred to the program by community corrections.
Tony Grannan of Loogootee said he is hoping to find a stable, good-paying job with his new skills. After previous jobs at Perdue Farms, and running heavy equipment in coal mining, he would like to get a job at Jasper Engines.
“I’ve learned how to work with others, problem solve and the importance of sequencing and staying consistent,” he said.
On time, ready to work
John Tooley is manager of business and industry for the VUJC program. Many workers today don’t understand modern manufacturing processes, he said. Attendance, being on time and working with others are all traits employers want.
“Manufacturers are super hungry for workers,” Tooley said. “We hear from them all the time, ‘We need more employees that will be here every day.’ It’s the number one need.”
For many years, manufacturers could count on workers who were job-ready.
“In Indiana you had people who had worked in farming or construction and they had the basic principles,” said Brad Rhorer, COO and chief talent officer at Conexus. “But as the workforce has aged, the new workers don’t have those basic competencies.
“If you don’t understand why you need to be at work every day or why you put the part on the car a certain way and in a set amount of time, then it’s hard to be successful in a manufacturing job.”
By simulating the production line, Catapult students are able to grasp the manufacturing philosophy.
One simulation had the class using Lego blocks to assemble a car, with each worker performing a different job. Mullis said the workers follow sequence sheets, designed for maximum efficiency, to do the work. As one worker added Lego “tires” and “headlights” to the cars, another checked for quality control, looking for any defects.
Tooley said in some of the simulations, the students aren’t given all the parts they need, requiring them to problem solve. It also illustrates the loss in productivity because of time spent getting the parts from the warehouse to the line.
Student Johnathan Dant of Loogootee said teamwork is the biggest skill he’s learned.
“We learned we might have to take on different roles if someone’s not here,” Dant said.
Edward Velarde of Martin County said he credits Catapult with giving him a new mindset.
“You need a good work ethic and you have to show up for work,” he said.
Student Josephine Henson of Daviess County said she now has a greater understanding of the manufacturing process. She previously worked at Perdue Farms making about $15 an hour.
“I want to work someplace where I’m able to move up,” she said.
Rhorer said Catapult students will be connected with employers and many will have multiple job offers by the time they complete the program.
“Our goal is 100% of them receive offers. If the class ends on Friday, we want them at a job on Monday,” Rhorer said.
Tooley said area employers like Jasper Rubber, Jasper Engines and Transmissions, furniture manufacturers, Farbest, Kimball Electronics and Kimball International have not been affected by work slowdowns and continue to seek workers.
“With the training they’ve got, these guys have a real shot at getting a great job,” Tooley said.
Catapult around Indiana
In working with justice-involved adults, Catapult is creating new opportunities and keeping those adults from going back into the system.
Among approximately 90 offenders in the first cohort that completed Catapult at Branchville, the recidivism rate dropped from 33.8% to 9.7%.
Other Catapult locations:
- Anderson
- Branchville
- Frankfort
- Greensburg
- Indianapolis
- Lafayette
- Wabash